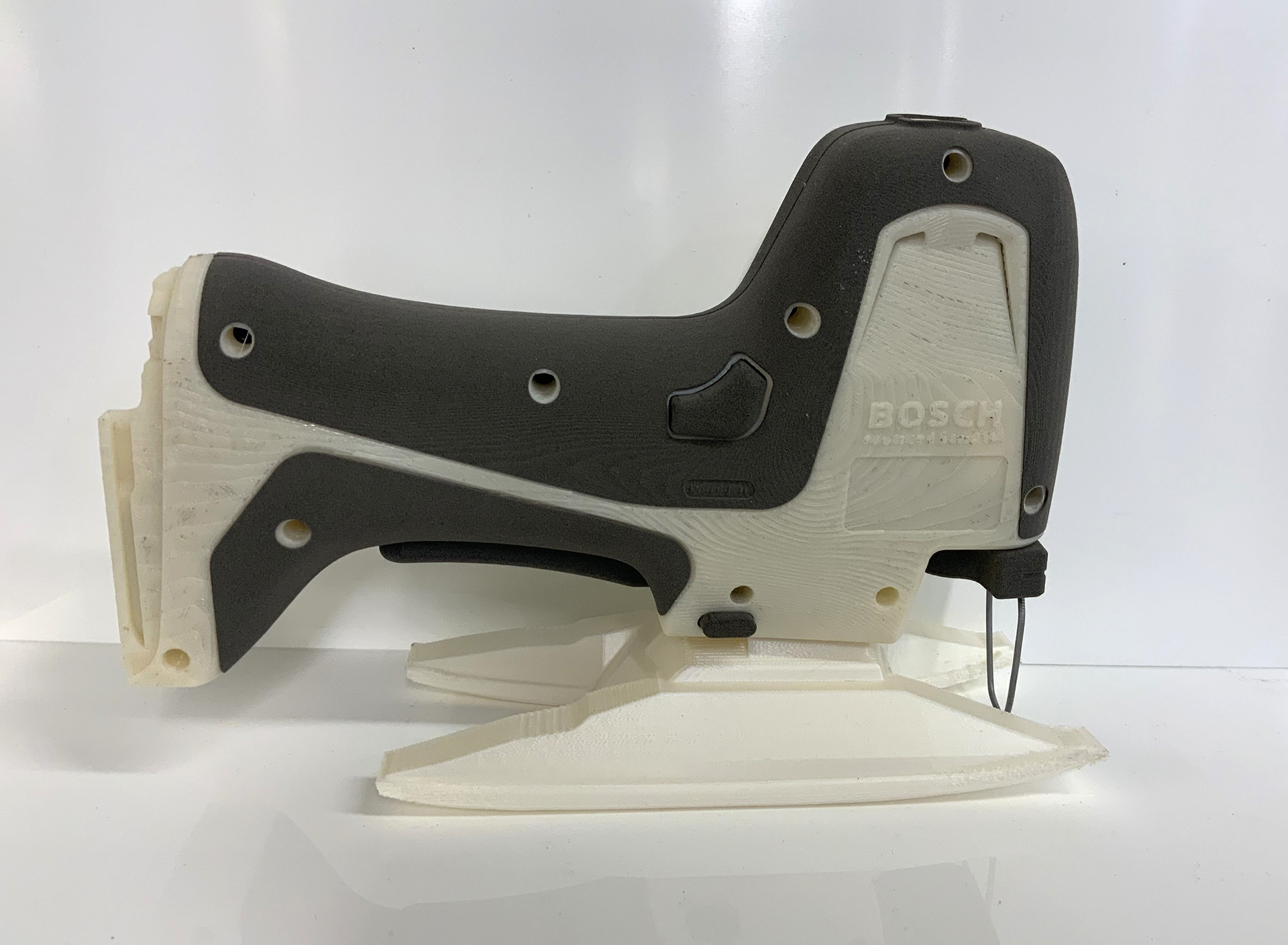
Model making is a real passion for me, making airfixes most of my life, I get real enjoyment from producing 3D models. The following models show the model development throughout the project. Although around 40 models were produced during the BOSCH 18V Jigsaw development, the following page shows the surface-level evolution of the models.
Cardboard modeling
Often used in the ideation stage of development, the flexibility of the cardboard, allows for quick changes to be implemented. Useful for testing the size and proportions of the models before proceeding into CAD.
The model on the right was produced for another concept and features a moving trigger to replicate the handle size accurately.
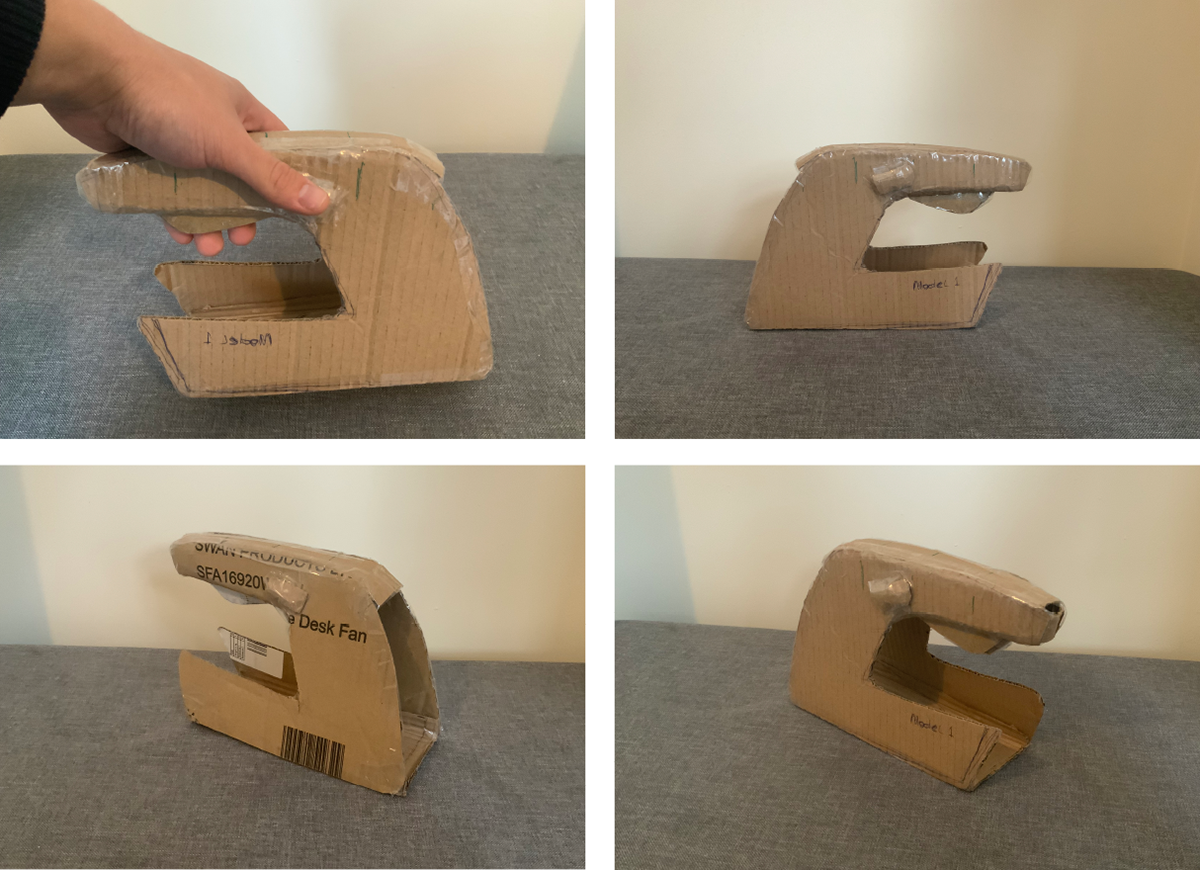
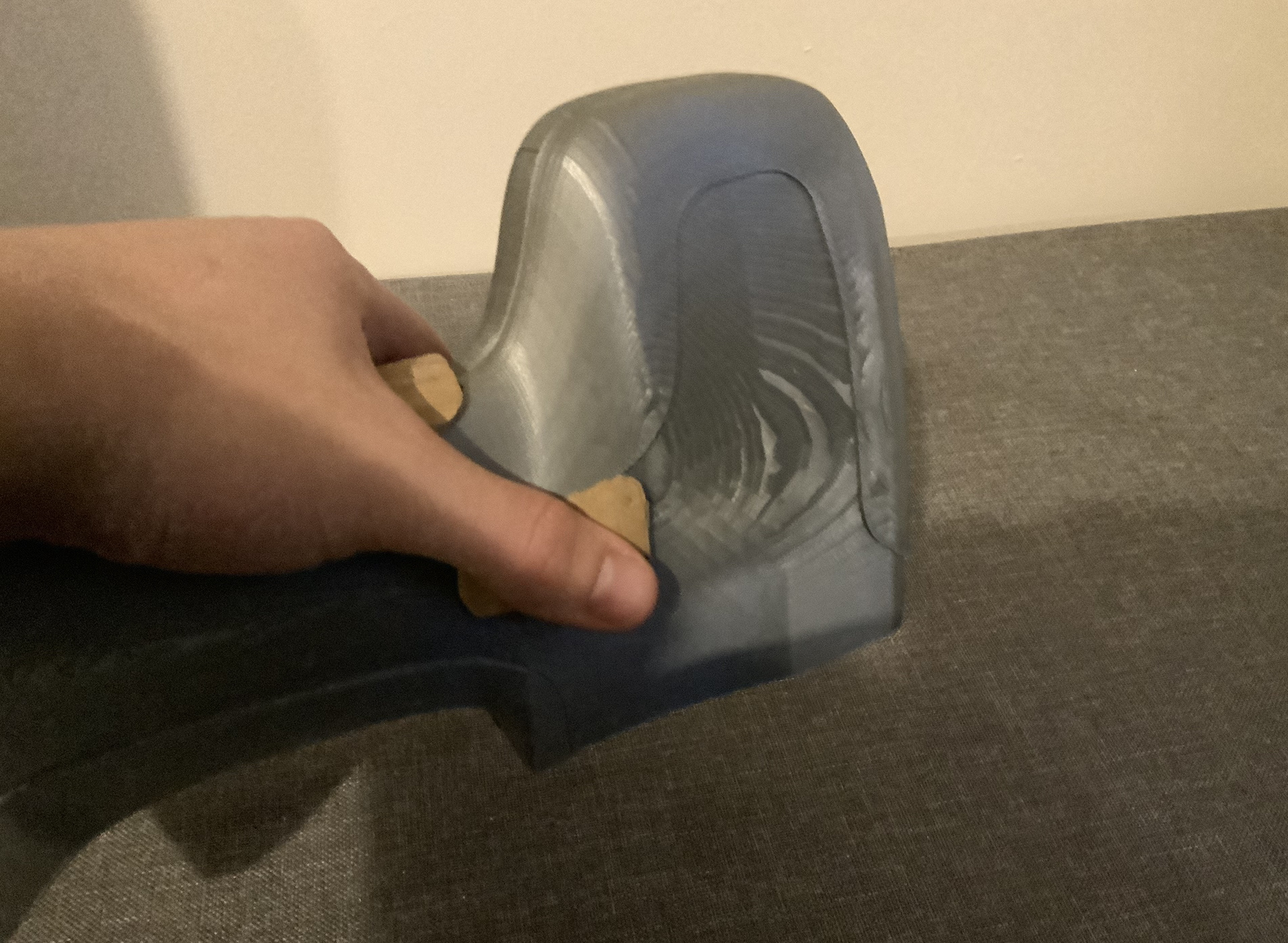
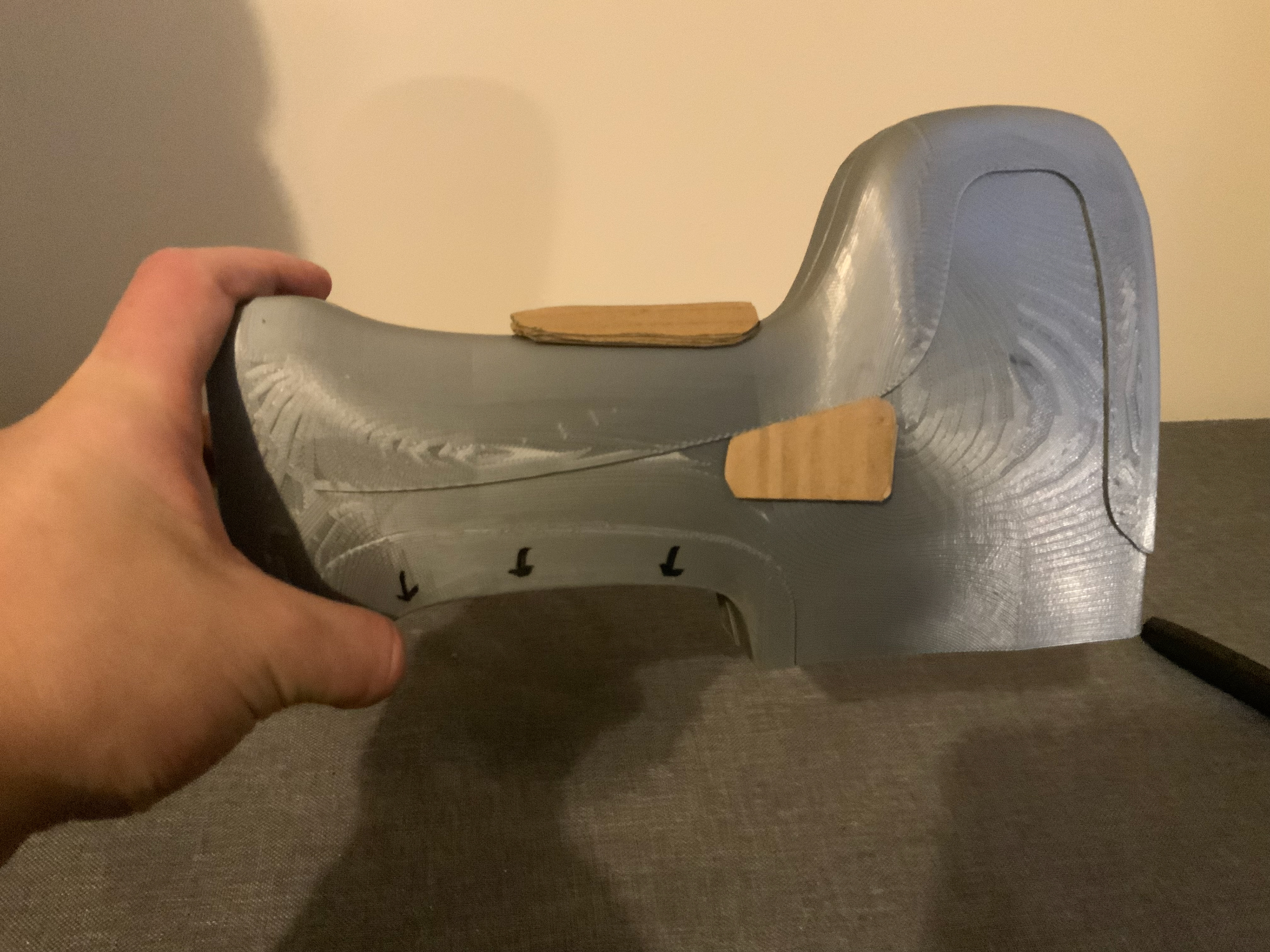
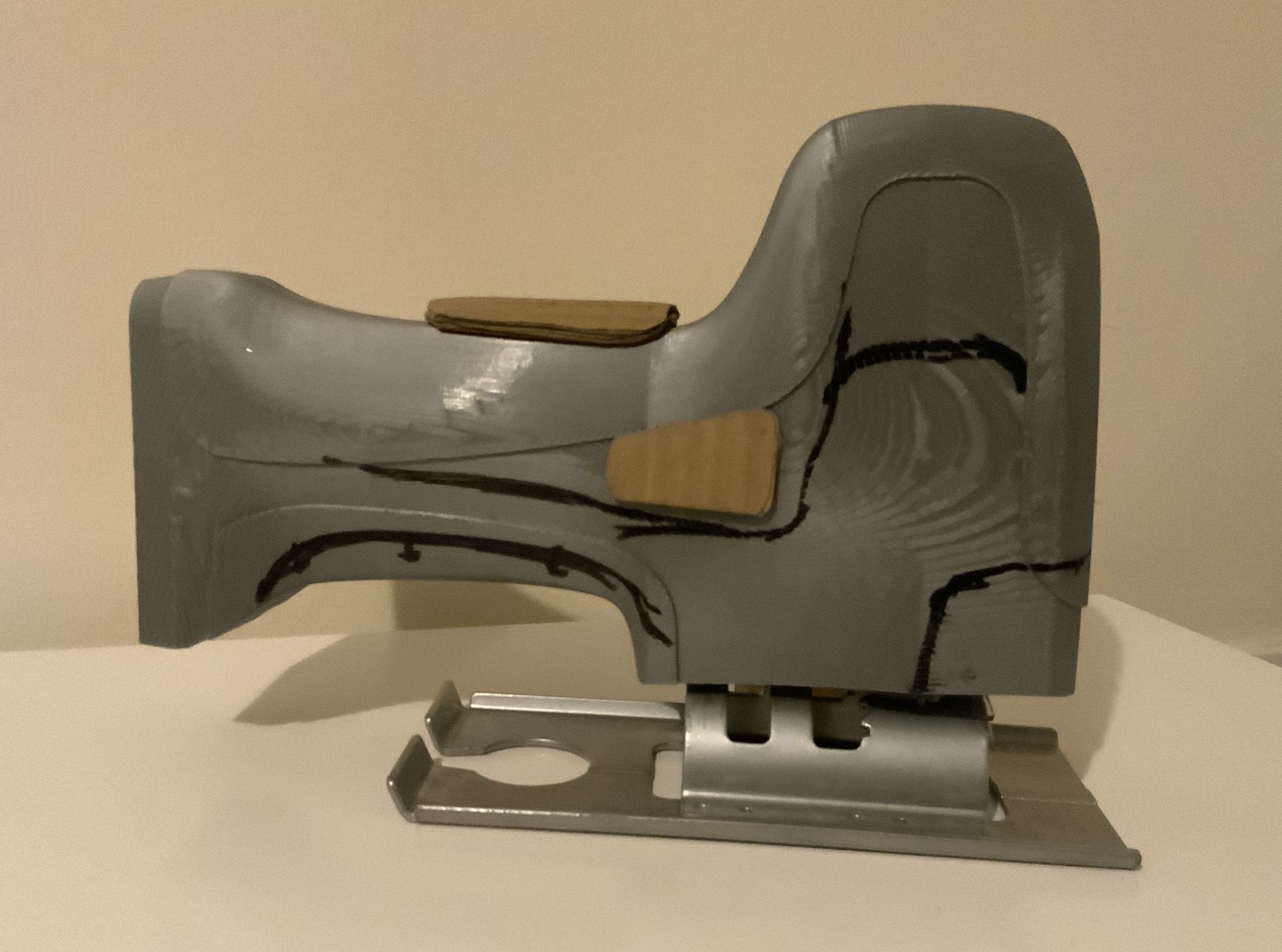
3D Print [PLA]
Once several iterations of cardboard models have been made, the dimensions are taken and translated into a CAD model, which is then printed.
A 3D printed model is brilliant for user testing as it does not flex like cardboard, providing an opportunity to hone into the ergonomics of the product.
The models on the left have been printed and cardboard has been temporally attached as the objective was finding the most idealistic place for buttons. Also, notice the pen marks. these were used to identify a change required.

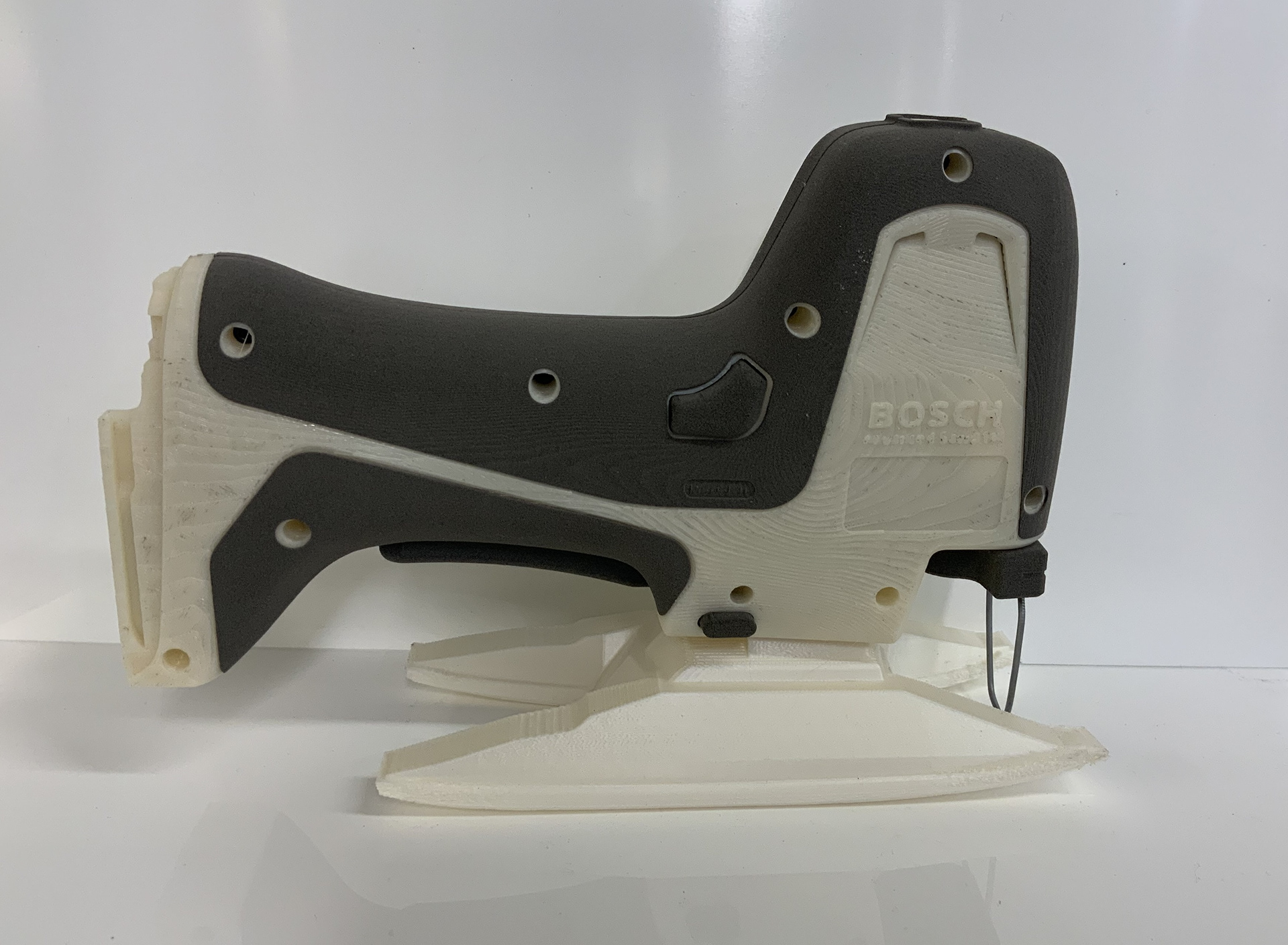
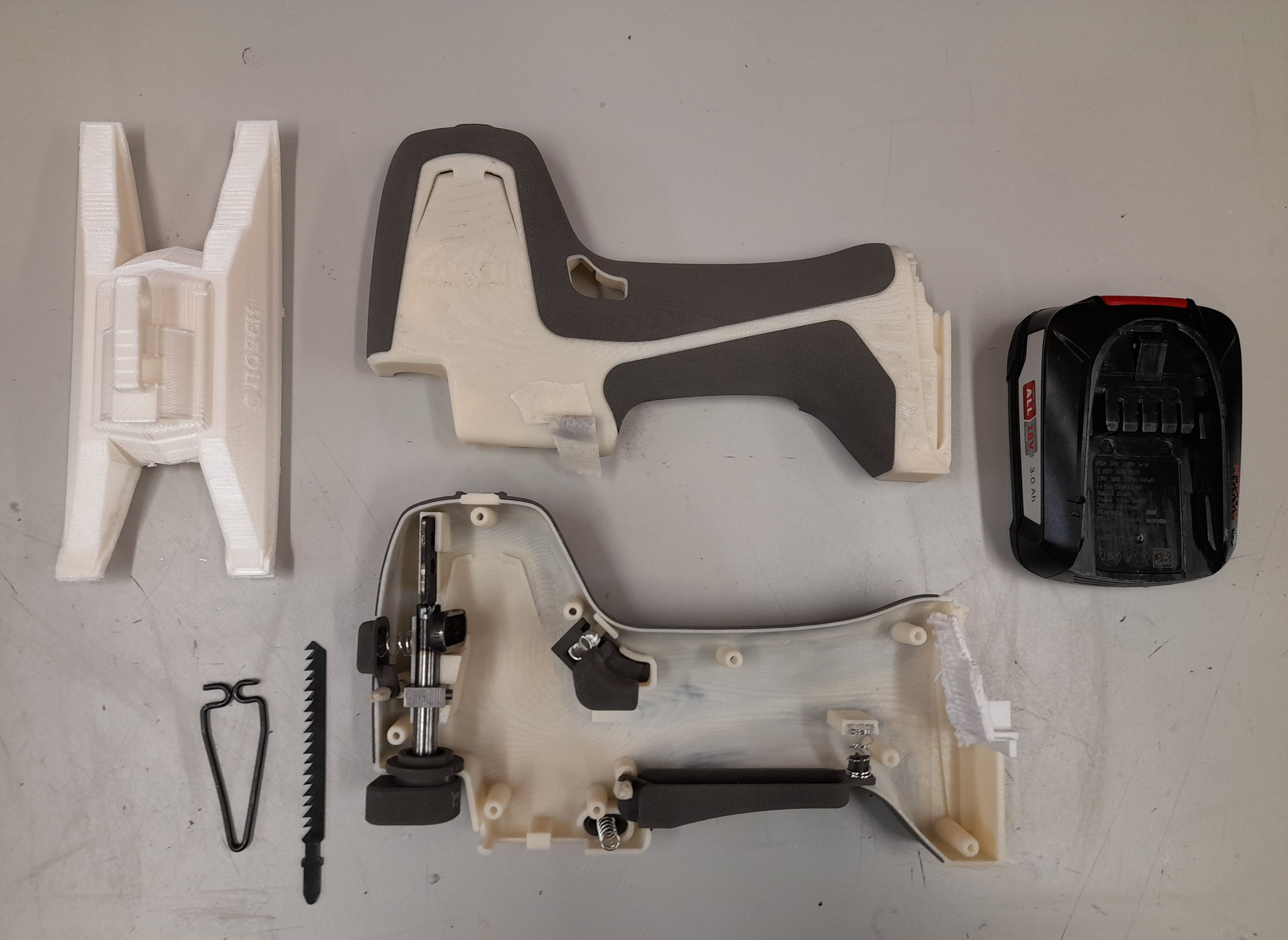
Presentation model
This model was made for the client, so they could evaluate the solution before proceeding to tooling for manufacture, as this is the final stage before changes are very costly. All components are designed to move, as this allows the client to fully evaluate the design.
The model above is made through a combination of FDM and SLA. The SLA printed parts were used for the interactive elements, such as the TPE and the buttons. This is because upon contact it has a softer feel. In the bottom right, there are the components that fit into the part, the motor assembly was not available.